مقایسه برش واترجت و برش پلاسما در زمینه برش فلزات و سایر مواد، نشان میدهد که تفاوتهایی بین این دو روش وجود دارد. این تفاوتها از نوع مواد گرفته تا سرعت برش و … متغیر است. با این حال، بهترین روش برش فلزات کدام است؟ برش واترجت یا برش پلاسما؟ در این مقاله به تفاوت بین برش واترجت و برش پلاسما از نظر اصول کار، مواد ایدهآل و هزینه به همراه ارائه ویدیو میپردازیم. برای خواندن ادامه مطلب، مجله کارآهن را دنبال کنید.
برش واترجت فلزات
سیستم برش واترجت با فشار دادن مخلوطی از آب و یک ماده ساینده (معمولا گارنت) از طریق یک نازل سرامیکی، مواد را تجزیه میکند. این مخلوط با فشار بیش از ۵۰۰۰۰ PSI از نازل خارج میشود و به آن اجازه میدهد تقریبا هر مادهای را برش دهد. به عبارت دیگر، سیستم برش واترجت یک سیستم فرسایش با سرعت بالا است.
در ویدیو زیر، میتوانید روش برش واترجت لوله فولادی را مشاهده کنید:
برش پلاسما چیست
بر خلاف برش واترجت، برش پلاسما از گازهای فشرده و الکتریسیته برای برش مواد استفاده میشود. این فرآیند شامل فشار دادن گاز فشرده از طریق یک دهانه منقبض با فشار بالا است که در آن با یک قوس الکتریکی تماس پیدا میکند.
هنگامی که با قوس الکتریکی که از طریق یک نازل ایجاد شده، تماس پیدا میکند، باعث واکنش میشود. گاز مورد استفاده برای این فرآیند بسته به نوع و ضخامت فلز میتواند نیتروژن، اکسیژن، آرگون و … باشد.
همچنین این گاز تا زمانی که به دمای مورد نظر برسد و وارد حالت چهارم ماده (یعنی پلاسما) شود، تحت حرارت قرار میگیرد. پلاسمای تولید شده در طی این فرآیند به قدری داغ است که میتواند فلز را با سرعت بالا برش دهد.
در ویدیو زیر، میتوانید روش برش پلاسما ورق فولادی را مشاهده کنید:
مقایسه واترجت و برش پلاسما از نظر مواد برش
عوامل موثر در انتخاب مواد برش واترجت و برش پلاسما عبارتند از:
۱- انعطافپذیری نسبت به مواد
در انعطافپذیری مواد، برش واترجت حرف اول را میزند. دلیل آن این است که میتواند تقریبا تمام مواد روی زمین را برش دهد. با این حال، مواد فلزی رایجی که میتواند برش دهد شامل فولاد، آلومینیوم و مس است. همچنین میتواند مواد دیگری مانند فوم، لاستیک، منسوجات و کاغذ را نیز برش دهد.
از طرف دیگر، روش برش پلاسما فقط میتواند فلزات رسانا را برش دهد. با اتصال الکترونها به گاز، قوس پلاسمایی را ایجاد میکند که برای برش استفاده میشود. با این وجود، در مقایسه با برش واترجت، محدودیتی در توانایی برش آن ایجاد میکند.
با این حال، از آنجایی که بیشتر فلزات رسانا هستند، در این روش، چالش برش وجود ندارد. فلزات متداول برش با استفاده از برش پلاسما عبارتند از آلومینیوم، فولاد، مس، آلیاژها، طلا، تیتانیوم و فولاد ضد زنگ.
بنابراین برای انتخاب مواد، برش واترجت نسبت به برش پلاسما بهتر است!
۲- ضخامت مواد برای برش
ضخامت مواد، عامل دیگری است که برش پلاسما را از برش واترجت متمایز میکند. دستگاه برش واترجت میتواند فولاد ضخیم یا فولاد ضد زنگ را تا ضخامت ۶ اینچ و برای موادی غیر از فلزات ۱۸ اینچ برش دهد. در ضمن، این تکنیک میتواند تا ۱۰۰ فوت ضخامت را در هنگام استفاده برای فرایندهایی مانند استخراج زغال سنگ کاهش دهد.
از سوی دیگر، برش پلاسما محدودیتی در عمق برش دارد. زیرا میتواند فولاد نرم و ضخیم را تنها تا ۶ اینچ برش دهد. با این حال، برای فلزات با ضخامت استاندارد، هر دو روش بهینه عمل میکنند.
۳- سیستم استفاده
مقایسه برش واترجت و برش پلاسما در زمینه فرآیند استفاده از هر دو روش متفاوت است. چنین تفاوتهایی عبارتند از:
بهرهوری و سرعت برش
خواص مواد که بر سرعت برش تأثیر میگذارند، شامل موارد زیر میشود:
- نوع ماده
- پیچیدگی برش
- ضخامت مواد
- دقت طراحی
هنگام برش یک ورق فلزی ضخیم، برش پلاسما با سرعت متوسط برش حدود ۲۰۰ اینچ در دقیقه سریعتر از برش واترجت عمل میکند. برعکس، بین برش واترجت و برش پلاسما، واترجت کند است و سرعت برش متوسط آن حدود ۱۵ اینچ در دقیقه است.
علاوه بر این، با سرعتهای بالاتر برش، بهرهوری در هنگام برش فلزات با روش برش پلاسما افزایش مییابد.
پیچیدگی برشها
هنگام ایجاد برشهایی که علاوه بر زاویهدار بودن، دارای فرورفتگی یا لبه برش صاف هستند، برش واترجت ایدهآل است. این روش برش، پیچیدگی بیشتری در فرآیند برش ایجاد و به سازندگان انعطافپذیری بیشتری میدهد.
به عبارت دیگر، برش اشکال پیچیده فلزات و سایر مواد با برش واترجت آسانتر انجام میشود. همچنین، یک برش واترجت پیشرفته، انتخاب فشار ایدهآل مورد نیاز برای بریدن فرورفتگیها در فلز را بدون برش آسانتر میکند.
از طرف دیگر، برش پلاسما باید مواد در حال برش را برای ایجاد طرح مورد نظر برش دهد. این امر ساخت تورفتگی و سایر برشهای پیچیده راغیرممکن می کند. با این حال، برش پلاسما برای برشهای نسبتا سادهتر ایده آل است.
اثرات تنش در حین برش
برش پلاسما باعث ایجاد پیچ و تاب، اعوجاج و سایر اشکال تنش به ماده برش میشود. این به دلیل دمای بالای تجربه شده در طول فرایند است. برعکس، دستگاه برش واترجت این نوع تنش را ایجاد نمیکند؛ زیرا حرارت شدیدی در طول فرایند ندارد.
بنابراین، اگر موادی را برش میزنید که به تنش حساس است، بهتر است از تکنیک برش پلاسما برای کیفیت بهتر خودداری کنید.
اثرات مربوط به گرما
اثرات مربوط به گرما در مواد ساخته شده با استفاده از روش برش پلاسما رخ میدهد. این در درجه اول به دلیل استفاده از دماهای بالا برای ذوب و برش مواد است. همچنین گازی که در طول فرآیند استفاده میشود، واکنش شیمیایی نزدیک به قسمت ذوب شده ایجاد میکند که اغلب رنگ و ترکیب شیمیایی آن قسمتها را تغییر میدهد.
با این حال، هنگام برش واترجت، اثرات مربوط به گرما وجود ندارد. زیرا این فرآیند شامل استفاده از گرما نمیشود. روش برش واترجت برای استفاده در مواردی که یکپارچگی و کیفیت کلی ضروری است، ایده آل به نظر میرسد.
سازگار با محیط زیست
مقایسه برش واترجت و برش پلاسما از نظر شرایط زیست محیطی نشان میدهد که برش اول به دلایل زیادی نسبت به برش پلاسما با محیط زیست سازگارتر است. اولا، روش برش واترجت شامل عملیات حلقه بسته است که در آن آب مورد استفاده برای برش در طی فرآیند بازیافت میشود. علاوه بر این، بازیافت تمام فلزات بریده شده در طول فرایند به عنوان فلز قراضه یا بازیافتی امکانپذیر است.
از سوی دیگر، برش پلاسما در طول فرایند بخار تولید کرده و در نتیجه بر جو تأثیر منفی میگذارد. همچنین فلز ذوب شده، تفاله یا نخاله تشکیل میدهد که محصول واکنش آن با گازها و آب است.
مصرف انرژی
برش پلاسما یک فرآیند انرژی بر است. این به دلیل فشار مورد نیاز برای استفاده از گاز و قوس الکتریکی در محل برش است. از طرف دیگر، تکنیک برش واترجت انرژی کمتری مصرف میکند زیرا در طول فرآیند فقط به پمپ آب با فشار بالا نیاز دارد.
به عبارت دیگر، دستگاههای برش پلاسما بیش از دو برابر دستگاههای برش واترجت، انرژی مصرف میکنند.
جدول مقایسه برش واترجت و برش پلاسما | |||||||||
نوع | سیستم برش | مواد قابل برش | نوع برشها | زمان برش | ضایعات برش | ایمنی | مصرف انرژی | سازگار با محیط زیست | کاربرد |
برش واترجت | فشار دادن مخلوطی از آب و یک ماده ساینده (معمولا گارنت) از طریق یک نازل سرامیکی | فولاد، آلومینیوم و مس | قابل استفاده برای برشهای پیچیده | طولانی | کمتر | بیشتر از برش پلاسما | کم | سازگار | صنایع معدنی، هوافضا و … |
برش پلاسما | استفاده از گازهای فشرده و الکتریسیته برای برش مواد | آلومینیوم، فولاد، مس، آلیاژها، طلا، تیتانیوم و فولاد ضد زنگ | قابل استفاده برای برشهای ساده | سریع | بیشتر | کمتر از برش واترجت | زیاد | عدم سازگاری | در ساخت و سازهای صنعتی و … |
برش پلاسما بهتر است یا برش واترجت؟
مقایسه برش واترجت و برش پلاسما از نظر پارامترهای مورد نیاز برای دست یافتن به نتایج نهایی مطلوب، عبارتند از:
۱- کیفیت محصول
تحمل و دقت از ویژگیهای بارز کیفیت محصول است. تلرانس فاصله برش از ناحیه مورد نظر، یک پارمتر مهم به حساب میآید. در نتیجه، تحمل برای برش پلاسما حدود ۰.۰۱۵ اینچ است. با این حال، برش پلاسما به طور قابل توجهی، تحمل بالاتری دارد.
از طرفی، برش واترجت دارای تحمل ۰.۰۰۱ اینچ است. به عبارت دیگر دقت بیشتری دارد. سطح تحمل و دقت برش واترجت به آن، کیفیت برش بهتری ارائه میدهد که در نتیجه نیاز به پرداخت کمتری است. بنابراین برای تضمین کیفیت بهتر محصول، برش واترجت نسبت به برش پلاسما، روش بهتری محسوب میشود.
۲- پرداختهای ثانویه
برش پلاسما به دلیل دقت کم، نیاز به پرداخت ثانویه دارد. تکمیل فلز ثانویه در این جنبه از سنگ زنی ریز حاصل میشود که به بهبود کیفیت لبه سطح برش کمک میکند.
از طرف دیگر، برش واترجت نیازی به پرداخت ثانویه ندارد زیرا سطح از قبل دارای دقت بالایی است. به عبارت دیگر، با انتخاب برش واترجت به جای برش پلاسما، در هزینه فرآیندهای تکمیل ثانویه صرفهجویی می کنید.
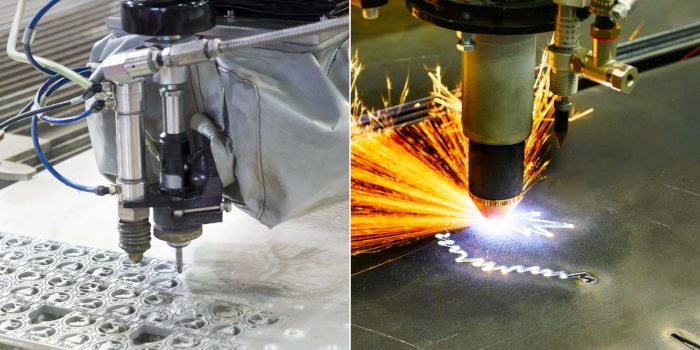
مقایسه برش واترجت و برش پلاسما از نظر دستگاه برش
در مورد دستگاه برش چطور؟ برش پلاسما از نظر ایمنی، طول عمر و تعمیر و نگهداری چگونه با دستگاه برش واترجت مقایسه میشود؟
۱- ایمنی
دستگاه برش واترجت نسبتا ایمنی بیشتری نسبت به دستگاه برش پلاسما دارد. این به دلیل عدم وجود دمای بالا و جریان باز است. همچنین، رتبه ایمنی برش واترجت خوب است. زیرا تجهیزات معمولا دارای یک بستر آبی هستند که فشار آب را حذف میکند.
از طرف دیگر، برش پلاسما، جریان الکتریکی و همچنین گرما را در دمای بسیار بالا تولید میکند. در نتیجه، این فرآیندی است که نیاز به آموزش زیادی از نظر ایمنی قبل از کار کردن با آن دارد. همچنین توصیه میشود تکنسینهایی که از این تکنیک استفاده میکنند از عینک ایمنی استفاده کنند. زیرا این روش برای چشم خطرناک است.
۲- طول عمر
مواد مصرفی مورد استفاده در برش پلاسما خیلی سریع فرسوده میشوند. به عنوان مثال، نازل تنها چند ساعت قبل از نیاز به تغییر دوام میآورد. درست است که زمان صرف شده برای ساخت با استفاده از این روش کوتاه است، اما سایش مواد به دلیل فشار و دمای بالای گازها سریعتر رخ میدهد.
از سوی دیگر، مواد مصرفی مانند نازل مورد استفاده در برش واترجت، طول عمر بیشتری دارند و اغلب حدود ۱۰۰ ساعت دوام میآورند. قطعاتی مانند پمپ فشار بیشتر عمر میکنند و تا حدود ۱۰۰۰۰ ساعت دوام دارند.
طول عمر کمتر برای مواد مصرفی مورد استفاده در برش پلاسما، هزینه های تولید را افزایش میدهد. زیرا جایگزینی مواد مصرفی فرسوده گران است. برعکس، برش واترجت ، نیاز کمی برای جایگزینی مواد مصرفی دارد که این مزیت یعنی، کاهش هزینه تولید.
۳- تعمیر و نگهداری
از آنجایی که هیچگونه تجهیزات پیچیدهای در برش واترجت وجود ندارد، تعمیر و نگهداری آن ساده است. همچنین عدم فرسودگی و پارگی مواد مصرفی باعث افزایش سهولت نگهداری از این دستگاه میشود. از طرف دیگر، تعمیر برش پلاسما به دلیل تغییر مکرر نازلها و الکترودهای فرسوده، کمی پیچیدهتر است.
کاربرد برش واترجت و برش پلاسما
برش واترجت تقریبا میتواند هر مادهای را با دقت بالا برش دهد. این مزیت به برش واترجت اجازه میدهد که در ساخت قطعات برای صنایع معدنی و هوافضا مشارکت داشته باشد.
از سوی دیگر، برش پلاسما از طریق موادی که میتوانند جریان الکتریسیته را هدایت کنند، مانند فولاد نرم و ضخیم، برش میدهد. به همین دلیل است که در ساخت محصولات مورد استفاده در ساخت و سازهای صنعتی و کاربردهای مشابه مورد استفاده قرار میگیرد.
مقایسه برش واترجت و برش پلاسما از نظر هزینه
هزینه عامل اصلی تمایز بین برش پلاسما و برش واترجت است. هنگام سرمایه گذاری در دستگاه برش پلاسما (CNC) در مقابل واترجت، پلاسما هزینه کمتری دارد.
از طرفی، هزینه دستگاه برش واترجت خیلی گران است. بنابراین برای تامین هزینههای اولیه، دستگاه برش پلاسما ارزان تر هستند.
همچنین، دستگاه برش پلاسما از نظر هزینههای عملیاتی کمتر، با بودجه کم، فرایند تولید در مقیاس بزرگ را آسانتر میکنند. هزینه عملیاتی برای برش واترجت به دلیل هزینه به دست آوردن مواد ساینده مورد استفاده در طول فرایند، بالاتر است.
بنابراین برای هزینههای اولیه و جاری، روش برش پلاسما بهتر از روش واترجت است.
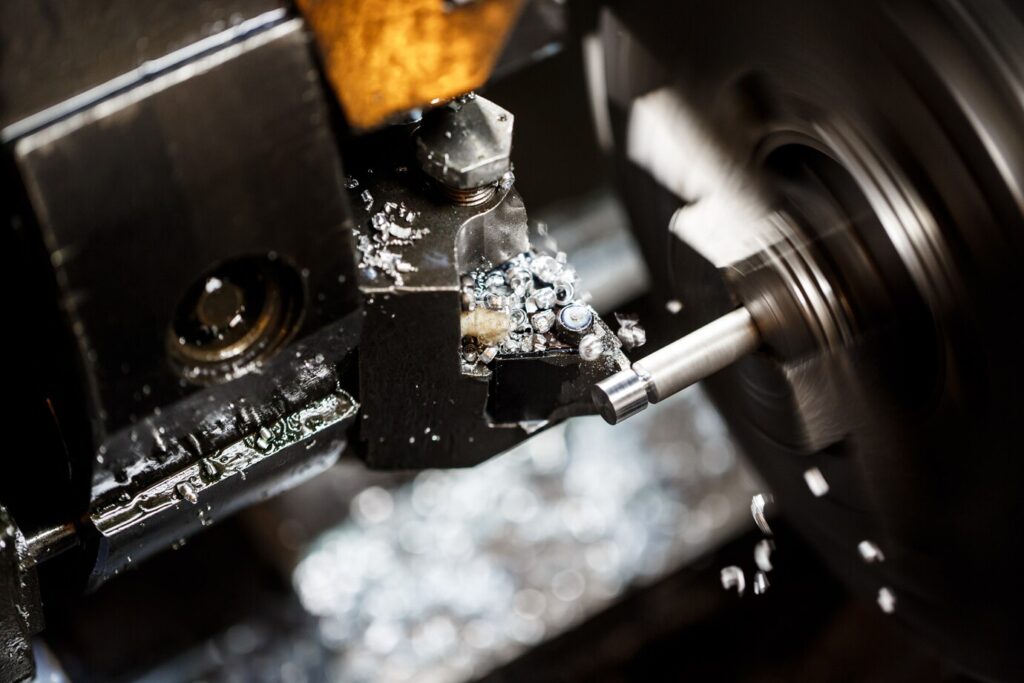
چه زمانی برش واترجت را به برش پلاسما ترجیح دهیم؟
هر دو روش برش، مزایا و معایب خود را دارند. پس اینجاست که این سوال مطرح میشود: چرا باید برش واترجت را به برش پلاسما ترجیح دهیم:
- کیفیت لبه فولادی تولید شده برش پلاسما با برش واترجت مطابقت ندارد. همچنین، پلاسما برش استانداردهای صنعت را برآورده نمیکند.
- به دلیل بازیافت آب و فلز که در طول فرآیند اتفاق میافتد یا میتواند رخ دهد، برش واترجت سازگارتر با محیط زیست است.
- برای برش موادی مانند گرانیت که به راحتی ذوب نمیشوند، ایده آل است.
- برای برش موادی که به راحتی در معرض گرما ذوب می شوند، گزینه مناسب است.
- برش واترجت در دمای پایینتر انجام میشود و هیچ وسیلهای گرم نمیشود.
کلام آخر
در این مقاله به مقایسه برش واترجت و برش پلاسما پرداختیم. سوال اصلی اینجاست که برش واترجت بهتر است یا برش پلاسما؟ به هر حال، اکنون که در مورد برش واترجت و برش پلاسما بیشتر میدانید، انتخاب مناسب برای برش فلزات شما آسان تر میشود. ما همچنین در مورد مزایای هر دو فرآیند نسبت به دیگری و همچنین تفاوت در فرایند کار، انتخاب مواد، کاربرد و هزینه بحث کردیم. برای کسب اطلاعات بیشتر، با کارشناسان کارآهن تماس بگیرید.
سوالات متداول
برش پلاسما فقط فلزات رسانای الکتریکی مانند فولاد نرم و ضخیم را برش میدهند. دستگاههای برش واترجت میتوانند هر نوع فلزی را با دقت بالا برش دهند.
برش واترجت یک لبه صاف و یکنواخت بدون سوراخ برای فلز شما ایجاد میکند. کیفیت لبه تولید شده با برش واترجت تابعی از سرعت، فشار، اندازه نازل و سرعت جریان ساینده است. در بسیاری از موارد واترجت نیاز به پرداخت ثانویه را از بین میبرد، بنابراین باعث صرفه جویی قابل توجهی در زمان و بهبود کارایی در کارگاه شما میشود.
در حالی که برش واترجت میتواند اغلب مواد فلزی را برش دهد، با این حال بیشتر از یک برش سنتی طول میکشد. بنابراین زمان برش واترجت طولانی است و در نتیجه گاهی بهرهوری از دست میرود.
همه چیز به نیازهای خاص شما بستگی دارد. اگر نیاز به برش سریع و دقیق انواع مواد دارید، احتمالا برش پلاسما بهترین انتخاب است. اگر به دنبال دستگاهی هستید که استفاده از آن آسان باشد و ضایعات زیادی تولید نکند، ممکن است دستگاه برش واترجت گزینه بهتری باشد.