آهن خام به عنوان ماده اولیه تولید فولاد استفاده میشود. تولید انواع آهن خام مانند آهن سفید، خاکستری و نیمه خاکستری در دو کوره بلند و قوس الکتریکی صورت میگیرد. در این مقاله به موضوع آهن خام به همراه انواع آهن خام و روشهای تولید آن میپردازیم. برای خواندن ادامه مطلب، مجله کارآهن را دنبال کنید.
آهن خام چیست؟
آهن خام یا چدن، محصول ذوب سنگ آهن با سوخت پرکربن و احیا کننده مانند کک است که معمولا با سنگ آهک به عنوان شار ترکیب میشود. زغال سنگ و آنتراسیت نیز به عنوان سوخت و احیا کننده مورد استفاده قرار میگیرند.
انواع آهن خام پس از تولید در کورههای بلند و قوس الکتریکی، وارد واحد ریختهگری میشود. در واحد ریختهگری نیز، با تبدیل شدن آهن خام به شمش فولادی، امکان استفاده از آن در فولادسازی به وجود میآید.
جدول ترکیب آهن خام
انواع آهن خام حاوی حداقل ۹۲ درصد آهن است و محتوای کربن بین ۳.۵ تا ۴.۷ درصد دارد. سایر ترکیبات آهن خام یا چدن در جدول زیر اشاره شده است:
جدول ترکیب آهن خام (درصد) | |||||
نوع آهن خام | کربن (C) | سیلیسیم (C) | منگنز (Mn) | سولفور (S) | فسفر (P) |
پایه | ۳.۵ تا ۴.۵ | ۱.۲۵ ≤ | ۱ ≤ | ۰.۰۵ ≤ | ۰.۰۸ تا ۰.۱۵ |
ریخته گری | ۲ تا ۲.۹ | ۰.۹ تا ۱.۹ | ۰.۱۵ تا ۱.۲ | ۰.۰۲ تا ۰.۲ | ۰.۰۲ تا ۰.۲ |
چدن نشکن یا داکتیل (خلوص بالا) | ۳ تا ۴ | ۱.۸ تا ۲.۸ | ۰.۱ تا ۱ | ۰.۰۱ تا ۰.۰۳ | ۰.۰۱ تا ۰.۱ |
سفید | ۱.۸ تا ۳.۶ | ۰.۵ تا ۱.۹ | ۰.۲۵ تا ۰.۸ | ۰.۰۶ تا ۰.۲ | ۰.۰۶ تا ۰.۲ |
خاکستری | ۲.۵ تا ۴ | ۱ تا ۳ | ۰.۲ تا ۱ | ۰.۰۲ تا ۰.۲۵ | ۰.۰۲ تا ۱ |
ماده اولیه برای تولید آهن خام
ماده اولیه آهن خالص چیست؟ برای تولید آهن خام یا چدن، ابتدا سنگ معدنی شامل زئولیت، هماتیت، مگنتیت، سیدریت و لیمونیت را از معادن استخراج میکنند. برای این که بتوان سنگ معدنی یا سنگ آهن را به آهن خام تبدیل کرد، باید آنها را به واحدهای فراوری کارخانه انتقال داد.
علاوه بر این، برای اینکه بتوان سنگ معدنی را به واحدهای فراوری انتقال داد، ابتدا باید آن را به سنگهای دانهبندی شده، کنسانتره و در مرحله آخر گندله تبدیل کرد. همچنین سنگ آهن کنسانتره ظاهر ریزی دارد .
وقتی سنگ آهن به گندله یا سنگ گرد تبدیل و با بنتونیت ترکیب شد، آن را به واحد فرآوری منتقل میکنند تا به آهن اسفنجی تبدیل شود. در ضمن سنگ آهن دانهبندی به دو حالت ریز (۱۰ میلیمتر) و درشت (۱۰ تا ۳۰ میلیمتر) به تولید میرسد.
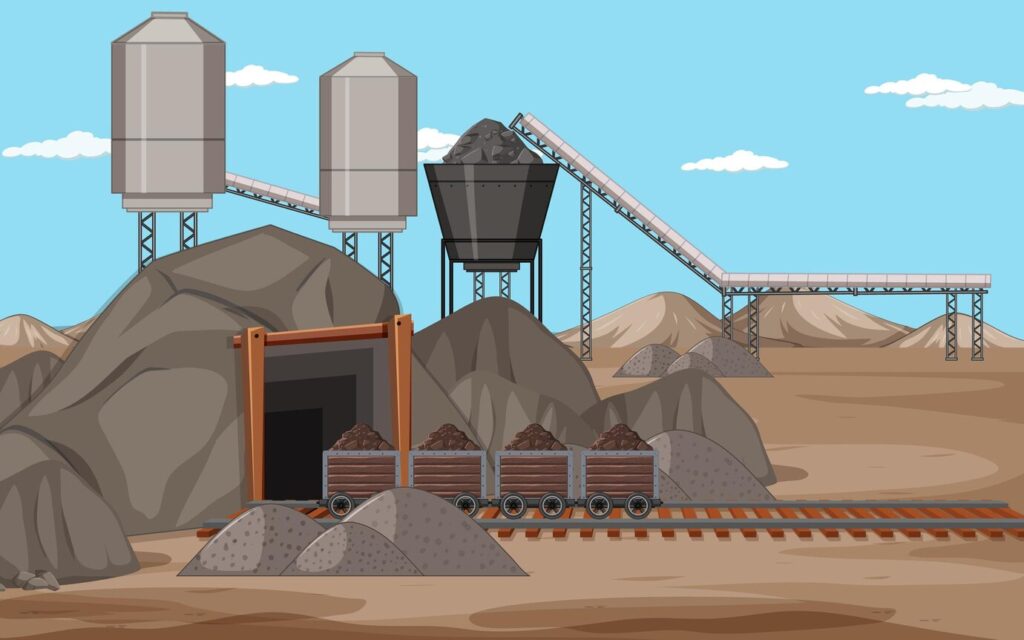
معادن سنگ آهن ایران
مهمترین معادن سنگ آهن ایران عبارتند از:
- معدن گلگهر در سیرجان استان کرمان
- معدن چادرملو در استان یزد
- معدن سنگ آهن چغارت بافق یزد
- معدن سنگان در استان خراسان
- معدن جلال آباد زرند
روشهای تولید آهن خام
تولید فولاد از زمان شروع خود راه طولانی را پیموده است. دلیل اصلی که چرا فولاد تغییر کرده است، شاید تکنیکها و فناوریهای پیرامون ساخت آن باشد. در ادامه نگاهی دقیقتر به اختراع مدرنی خواهیم داشت که انقلابی در نحوه تولید، بازیافت و استفاده مجدد از پرمصرفترین فلز روی کره زمین ایجاد کرده است.
اولین گام این است که بفهمیم کوره چیست و چه هدفی در فرآیند فولادسازی دارد. کوره نه تنها برای ذوب کردن فولاد، بلکه برای حذف مواد ناخواستهای که کیفیت فلز را کاهش میدهند نیز استفاده میشوند. این فرآیند ذوب میتواند برای حذف اولیه فلز از سنگ معدن خام یا ذوب فلز موجود برای اصلاح و استفاده مجدد از آن استفاده گردد.
علاوه بر این، کورهها نه تنها در ابتدای عمر یک فلز، بلکه در هر بار تغییر کاربری آن نقش بسیار مهم ایفا میکند. از آنجایی که هدف یک کوره متالورژی گرم کردن و ذوب انواع آهن خام است، راههای مختلفی برای رسیدن به این هدف وجود دارد. دو روش اصلی تامین این گرما با استفاده از کوره بلند یا کوره قوس الکتریکی است.
۱- روش کوره بلند
تاریخچه کورههای بلند را میتوان تا چین باستان (در مقیاس کوچکتر) ردیابی کرد. کورههای بلند از کک یا زغال سنگ خالص برای ذوب سنگ آهن و ایجاد انواع آهن خام در دمای ۳۰۰ درجه سانتیگراد استفاده میکنند.
سپس اکسیژن به کوره تزریق میشود تا محتوای کربن فولاد کاهش یابد و ناخالصی ها حذف شود. کورههای بلند فضای زیادی را اشغال کرده و دی اکسید کربن زیادی تولید میکنند، اما ساخت فولاد به این روش، آسانتر است.
۲- روش کوره قوس الکتریکی
کورههای قوس الکتریکی یا EAF، تجسم بسیار جدیدتری از کوره متالورژیکی هستند و (همانطور که از نام آنها پیداست) با برق کار میکنند. EAFها ضایعات، فلزات بازیافتی و آهن اسفنجی را با عبور جریان الکتریکی از الکترودهای گرافیت (یا گاهی اوقات کربن) ذوب کرده و قوس ایجاد میکنند.
کوره قوس الکتریکی مقدار زیادی گرما را از خود ساطع میکند که باعث ذوب شدن محتویات کوره میشود. این روش نه تنها انواع آهن خام را به سرعت تولید میکنند، بلکه معمولا هزینه اولیه نسبتا پایینتری نسبت به کوره بلند دارند.
بنابراین آهن اسفنجی یا فلزات بازیافتی (قراضه آهن)، با کک، بنتونیت و آهک وارد کوره قوس الکتریکی میشود. سپس ناخالصیها حذف و مواد به دست آمده، وارد واحد ریختهگری میگردد. در واحد ریختهگری، شمش فولادی تولید میشود.
تفاوت کوره بلند و کوره قوس الکتریکی
در حالی که محصول نهایی انواع آهن خام هر یک از این دو روش مشابه است، به وضوح بین قابلیتها و فرآیند آنها تفاوتهایی وجود دارد. با مقایسه هر نوع کوره، تفاوتهای عمده عبارتند از:
۱- مواد اولیه کوره
کوره بلند میتواند سنگ آهن خام و همچنین فلز بازیافتی را ذوب کنند، در حالی که کوره قوس الکتریکی فقط فلزات بازیافتی یا ضایعات را تحت فرایند ذوب قرار میدهد.
۲- منبع تغذیه کوره
کوره بلند عمدتا از کک جهت تامین انرژی مورد نیاز برای گرم کردن فلز استفاده میکند، در حالی که کوره قوس الکتریکی از برق برای انجام این کار بهره میگیرد.
۳- اثرات زیست محیطی
فولاد یکی از بازیافتترین مواد روی کره زمین است و در واقع قابلیت بازیافت ۱۰۰ درصدی دارد. همانطور که در بالا ذکر شد، کوره قوس الکتریکی راه بسیار تمیزتری را برای تولید فولاد فراهم میکند.
به طور سنتی، سوختهای فسیلی مانند زغالسنگ برای تامین انرژی این کورههای بلند استفاده میشد، اما اکنون، فناوری این امکان را به وجود آورده است که این ماده حیاتی را به روشی پایدارتر تولید کرد که با ویژگیهای سازگار با محیط زیست محصول همخوانی دارد.
با این حال، به دلیل سوختهای مورد استفاده برای هر یک، کوره قوس الکتریکی میتواند تا ۸۵ درصد کمتر از کوره بلند در حین تولید انواع آهن خام، دی اکسید کربن ایجاد کند.
۴- کارایی
کوره قوس الکتریکی همچنین بسیار سریعتر از کوره بلند به دمای بالا میرسد و میتواند سریعتر ذوب شود و انواع آهن خام را تولید کند. همچنین کنترل دقیقتری بر دما در مقایسه با کوره بلند دارد.
۵- هزینه
کوره قوس الکتریکی نسبت به کوره بلند هزینه کمتری دارد و فضای کمتری را در کارخانه اشغال میکند.
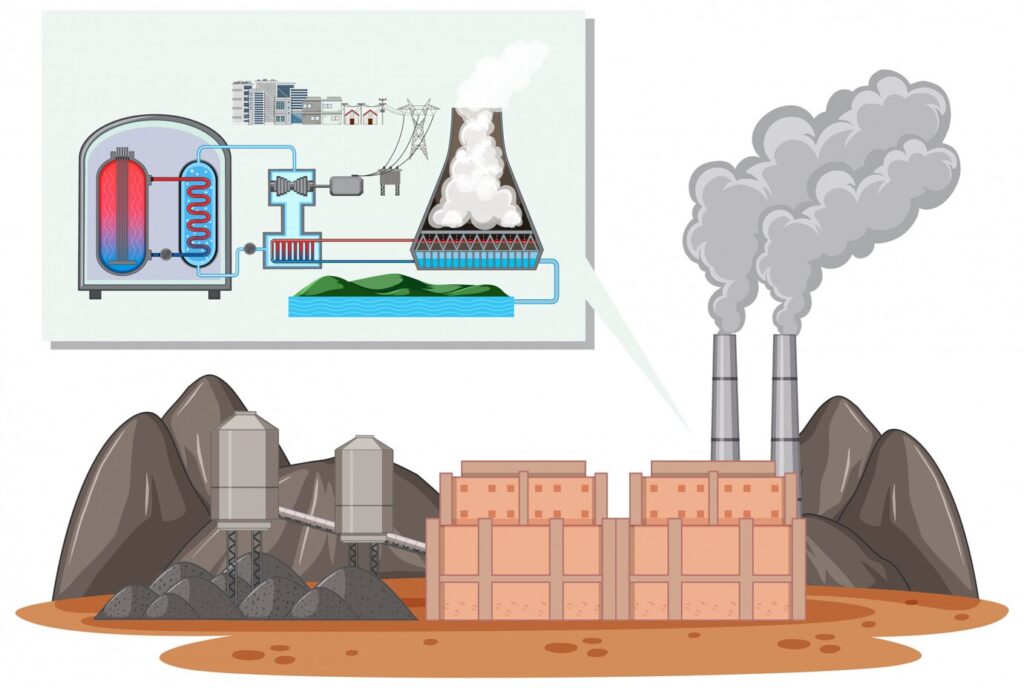
انواع آهن خام
آهن خام به دو دسته ترکیب و ناخالصی به همراه رنگ و ظاهر تقسیمبندی میشود که در ادامه به هر کدام از آنها میپردازیم:
۱- انواع آهن خام از نظر ترکیب و ناخالصی
ترکیب و ناخالصی آهن خام بر خواص و کارکرد آن تاثیر میگذارد؛ به همین دلیل، آن را به لحاظ ترکیب و میزان ناخالصیهایش طبقهبندی کردهاند. از انواع آهن خام از نظر ترکیب و ناخالصی میتوان به موارد زیر اشاره کرد:
آهن خام پایه
آهن خام پایه یا Basic pig iron، یه نوع ماده اولیه برای تولید فولاد است. این نوع آهن در کوره قوس الکتریکی مورد استفاده قرار میگیرد. بنابراین شما نمیتوانید از آهن خام پایه در کوره بلند استفاده کنید.
آهن یا چدن خام ریخته گری
در زبان انگلیسی به آهن یا چدن خام ریختهگری، Foundry pig iron گفته میشود. این نوع آهن به عنوان آهن خام هماتیت معروف است. آهن خام ریختهگری به عنوان مواد اولیه تولید چدن خاکستری مورد استفاده قرار میگیرد. برای تولید آن، از کوره کوپل استفاده میشود
آهن یا چدن خام خلوص بالا
آهن یا چدن خام با خلوص بالا یا High purity pig iron، یک نوع ماده اولیه تولید چدن با خلوص یا عیار بالا است که در بازار آهن به نام آهن خام کروی شناخته میشود. اصولا استفاده از چدن خام با خلوص بالا برای تولید چدن نشکن کاربرد دارد.
۲- انواع آهن خام از نظر رنگ و ظاهر
آهن خام از نظر رنگ و ظاهر دستهبندی جداگانهای دارد. از این رو، در زمان خریدانواع آهن خام باید به ظاهر و رنگ آن توجه داشته باشید. این محصول در سه رنگ سفید، خاکستری و نیمه خاکستری موجود است که در قسمت زیر، توضیحات آنها را آوردهایم:
آهن خام سفید
آهن خام سفید چگونه ساخته میشود و چه ویژگیهایی دارد؟ ابتدا باید گفت که آهن خام سفید یک رنگ نقرهای دارد که در نقطه ذوب آن ۱۱۰۰ درجه سانتیگراد است. این محصول به عنوان ماده اولیه تولید فولاد مورد استفاده قرار میگیرد.
از طرفی، وقتی سرعت سرد شدن آهن مذاب به گونهای باشد که هیچگونه گرافیتی در آن تشکیل نشود، اینجاست که آهن سفید سخت، ترد با مقدار سیلیس کم و منگنز زیاد دست میآید. همچنین سطح شکست آهن سفید به صورت روشن و ریزدانه است.
آهن خام خاکستری
همانطور که از نام این نوع آهن پیداست، ظاهر خاکستری رنگ دارد که دارای مقدار سیلیس بالایی است. به همین دلیل خمش تردتری نسبت به سایر انواع آهن خام دارد. بنابراین مهمترین کاربرد آن برای چدن ریزی در نظر گرفته میشود.
علاوه بر این، وقتی سرعت سرد شدن آهن مذاب به آرامی صورت گیرد، اینجاست که کربن به شکل گرافیت ایجاد میشود. بنابراین آهن خاکستری در نقطه ذوب ۱۲۰۰ درجه سانتیگراد به دست میآید. همچنین سطح شکست آهن خام خاکستری درشت دانه است که نسبت به آهن خام سفید، نرمی بیشتری دارد.
آهن خام نیمه خاکستری
آهن نیمه خاکستری یا آهن خام به رنگ خاکستری روشن، اغلب در تولید چدن و فولاد مورد استفاده قرار میگیرد. این نوع آهن دارای ویژگیهای مابین یا ترکیبی از آهن خام سفید و خاکستری است. زیرا نه سفید است و نه خاکستری خالص؛ بلکه رنگ آن ترکیبی از هر دو آهن خام اشاره شده است.
خواص مکانیکی آهن خام
در جدول زیر به برخی از خواص مکانیکی کلیدی برای گریدهای مختلف چدن یا انواع آهن خام اشاره میکنیم.
جدول خواص مکانیکی آهن خام یا چدن | ||||
نوع | سختی برینل | استحکام کششی | مدول الاستیسیته | درصد کشیدگی (در ۵۰ میلیمتر) |
آهن خاکستری کلاس ۲۵ | ۱۸۷ | Ksi 29.9 | ۱۶.۱ Msi | – |
آهن خاکستری کلاس ۴۰ | ۲۳۵ | Ksi 41.9 | ۱۸.۲ Msi | – |
چدن داکتیل گرید ۶۰-۴۰-۱۸ | ۱۳۰ تا ۱۷۰ | Ksi 60 | ۲۴.۵ Msi | – |
چدن داکتیل گرید ۱۲۹-۹۰-۰۲ | ۲۴۰ تا ۳۰۰ | Ksi 120 | ۲۵.۵ Msi | – |
آهن با گرافیت فشرده گرید ۲۵۰ | Max 179 | Ksi min 36.2 | – | ۳ |
آهن با گرافیت فشرده گرید ۴۵۰ | ۲۰۷ تا ۲۶۹ | Ksi min 65.2 | – | ۱ |
کاربرد آهن خام
مهمترین و اصلیترین کاربرد انواع آهن خام استفاده در واحدهای ریختهگری برای تولید شمش، بیلت و اسلب فولادی است. این محصول به صورت مایع وارد کارخانههای فولادی میشود. بنابراین آهن خام به عنوان ماده اولیه محصولات فولادی در واحدهای نورد مورد استفاده قرار میگیرد.
کلام آخر
در این مقاله به موضوع آهن خام و انواع آن پرداختیم. آهن خام از ماده اولیه سنگ آهن و تبدیل آن به آهن اسفنجی تولید میشود. علاوه بر استفاده آهن اسفنجی برای تولید انواع آهن خام، از ضایعات آهنی نیز برای تولید این محصول بهره میگیرند. انواع آهن خام شامل آهن خام خاکستری، سفید و نیمه خاکستری است که برای تولید فولاد استفاده میشود.
سوالات متداول
به آهن خام، چدن نیز گفته میشود.
آهن خام از نظر رنگ به سه دسته آهن خام سفید، نیمه خاکستری و خاکستری تقسیم میشود.
انواع آهن خام به روش کوره بلند و کوره قوس الکتریکی تولید میشود.
مواد اولیه مورد نیاز برای تولید انواع آهن خام شامل سنگ آهن و کک است. بسته به نوع ناخالصیهای موجود در آهن، شارهای مختلفی اضافه میشود. به عنوان مثال سنگ آهک (برای سنگ آهن سیلیسی) یا فلدسپات (برای سنگ آهن آهکی). شار، ناخالصیهای موجود در آهن را به سربارهای که به راحتی ذوب میشود، تبدیل میکند.