نورد سرد فرآیندی است که طی آن فلز در دماهای کمتر از دمای تبلور مجدد از طریق غلتکها عبور کرده تا فلز فشرده و قدرت تسلیم و سختی آن افزایش یابد. در راستای ایجاد سختی بیشتر، استحکام بالاتر و شکلپذیری بهتر، برخی از محصولات فولادی نظیر ورق فولادی (ورق روغنی، ورق گالوانیزه و غیره)، تسمه فولادی و میلگرد، تحت فرایند نورد سرد قرار میگیرند. در این مقاله سعی داریم تا به موضوع نورد سرد بپردازیم. برای خواندن ادامه مطلب، مجله کارآهن را دنبال کنید.
نورد سرد
یکی از انواع نورد، نورد سرد فرایندی است که طی آن ضخامت فلز از طریق غلتکها در دماهای کمتر از دمای تبلور مجدد، کاهش پیدا میکند. هدف از این فرآیند، ایجاد ورقهای فولادی نازک با دقت ابعادی، کیفیت و ظاهر عالی سطح برای کاربردهای مختلف است.
در این فرایند به واسطه فشرده شدن فلز، دانهها جهت میگیرند و با ریز شدن دانهها، میزان سختی و استحکام نمونه بهبود مییابد. از طریق نورد سرد، محصولاتی مانند ورق فولادی (ورق روغنی، ورق گالوانیزه و ورق رنگی)، تسمه فولادی و میلگرد نیز تولید میشود.
علاوه بر این، نورد سرد در ابتدای خط محصولات تخت یا همان ورق فولای انجام میشود. برای اینکه بدانیم فولاد نورد سرد شده چیست، فلز مورد نظر ابتدا تحت نورد گرم قرار میگیرد تا ضخامت آن کاهش پیدا کند.
سپس به مرحله نورد سرد میآید تا سطح آن کشیده شود. با کشیده شدن سطح ورق، ضخامت آن نیز کاهش پیدا میکند و ما با یک ورق نازک مواجه خواهیم بود. بنابراین محصولات تولید شده تحت نورد سرد نسبت به نورد گرم، نه تنها نازکتر هستند بلکه استحکام بالاتری نیز دارند.
بیشتز بخوانید:
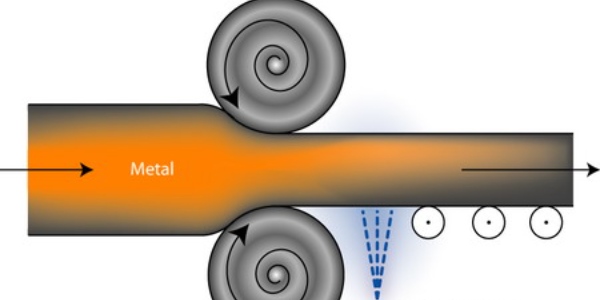
نورد سرد به انگلیسی
در زبان انگلیسی به نورد سرد، Cold rolling گفته میشود.
کاربرد نورد سرد
نورد سرد یک فرایند سختکاری شده است که برای تغییر ساختار فلزات استفاده میشود. یکی از کاربردهای این فرآیند، تبدیل کردن فولاد معمولی به فولاد ضد زنگ است. فولاد ضد زنگ به عنوان یک ماده خام، کاربردهای گستردهای در مهندسی پزشکی، هوافضا و صنعت خودروسازی دارد.
همچنین فولاد تولید شده تحت نورد سرد در دنیای ساختوساز، معمولا برای تولید سازههایی مانند تیرها، ستونها و مقاطع استفاده میشود.
محصول نهایی ورق فولادی تولید شده تحت فرایند نورد سرد در ساخت سولههای فولادی، ساختمانهای صنعتی، مخازن فولادی و گاراژها نیز مورد استفاده قرار میگیرد.
دیگر موارد پر کاربرد فولاد نورد سرد عبارتند از:
- مبلمان فلزی
- تجهيزات ساختمانی
- قطعات سازهای
- لوازم خانگی (ماشین ظرفشویی، ماشین لباسشویی، اجاق گاز، یخچال، فریزر و غیره)
- آبگرمکن
- ظروف فلزی
- پرههای فن
- ماهیتابه
- کابینت فلزی آشپزخانه
- کمد فلزی
- دوچرخهسازی
- دستگاههای الكتريكی مخازن
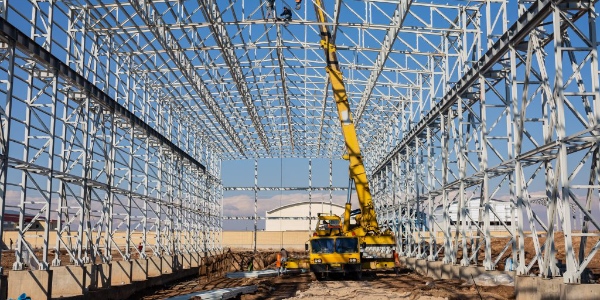
مقاطع تولید شده در فرآیند نورد سرد
ورق فولادی یکی از مهمترین محصولات تولید شده در طول فرآیند نورد سرد است که در صنایع مختلف کاربرد دارد. این محصول در طول فرآیند نورد سرد به یک ورق نازک تبدیل میشود تا بتوان از این محصول در صنایع مختلف به ویژه صنعت ساختمانسازی استفاده کرد.
از جمله مقاطع تولید شده در فرآیند نورد سرد میتوان به مقاطع عریض، مقاطع باز و مقاطع بسته اشاره کرد:
- مقاطع باز شامل تیرآهن، سپری و ناودانی
- مقاطع بسته شامل انواع لولهها (استیل و غیره) و انواع پروفیل
- مقاطع عریض شامل انواع ورق (مانند ورق روغنی)
مزایا و معایب نورد سرد
همه فرآیندهای فولادسازی شامل حرارت دادن فولاد به دمای تبلور مجدد یا بالاتر از آن نیست. به عنوان مثال، نورد سرد در دمای محیط انجام میشود. جای تعجب نیست که این فرایند برای رول کردن و ساخت ورق فولادی در دمای محیط به فشار بیشتری نیاز دارد.
از آنجایی که فولاد نورد سرد بسیار کمتر از دمای تبلور مجدد فولاد دستکاری میشود، با این حال، مزایای متعددی را ارائه میدهد که شامل استحکام و سختی بالا به همراه سطح با دقت ابعادی بالا و عاری از اکسید و پوسته (سطح صاف و قدرتمند) است.
۱- استحکام بالا
فولاد نورد سرد استحکام بالاتری نسبت به فولاد نورد گرم دارد. همانطور که غلتکها، فولاد را در دمای محیط فشرده میکنند، این محصول به دلیل سخت شدن، کرنش قویتری به خود میگیرد.
با این وجود، پرسش اینجاست که استحکام فولاد نورد سرد چقدر بیشتر از نورد گرم است؟ اگرچه استثنائاتی وجود دارد، اما استحکام فولاد نورد سرد معمولا حدود ۲۰ درصد بیشتر از همتای خود یعنی نورد گرم است.
۲- تحمل سختی بیشتر
در فلزکاری، اصطلاح «تلرانس» به ضخامت کلی فلز اشاره دارد. فولاد نورد سرد معمولا نازکتر از فولاد نورد گرم (بدون کاهش مقاومت) است و میتواند ضخامت فولاد را تا ۵۰ درصد کاهش دهد. در نتیجه، نورد سرد تلورانسهای سختتری نسبت به سایر فرآیندهای فولادسازی ارائه میدهد.
۳- سطح بهبود یافته
فولاد نورد سرد علاوه بر استحکام بیشتر، سطح یا روکش بهتری نیز نسبت به نورد گرم دارد. همچنین نسبت به فولاد نورد گرم، صافتر است و عیوب سطحی کمتری به خود میگیرد.
این مزیت نه تنها ظاهر فولاد نورد سرد را زیباتر از فولاد نورد گرم نشان میدهد، بلکه محصول تولید شده در طول این فرآیند را به ماده مناسبتری برای کاربردهای خاص مانند ساخت پل تبدیل میکند.
همانطور که میبینید، فولاد نورد سرد مزایای متعددی را ارائه میدهد که برخی از آنها شامل استحکام بالا، سطح بهبود یافته، تلرانسهای سختتر و… میشود. با این حال فرایند نورد سرد معایبی را شامل میگردد.
در مقایسه با فولاد نورد گرم، فولاد نورد سرد معمولا هزینه بیشتری برای تولید دارد. به همین خاطر برای بسیاری از شرکتهای فولادی، نورد گرم را به فرآیند جذابتری تبدیل میکند.
یکی دیگر از معایب فولاد نورد سرد، چکشخواری کم آن است. تغییر شکل و دستکاری شکل فولاد نورد گرم آسانتر است؛ زیرا این فرآیند نیاز به حرارت دادن فولاد تا دمای تبلور مجدد یا بالاتر از آن دارد.
با این حال، نورد سرد شامل فشردهسازی فولاد در زیر غلتکها در دمای محیط است و در نتیجه شکل دادن به آن را دشوارتر میکند.
بیشتر بخوانید: همه چیز درباره لوله استیل ۳۰۴ به همراه قیمت
تجهیزات نورد سرد
درباره این موضوع که نورد سرد چیست، پیشتر اشاره کردیم؛ با این حال نورد سرد یکی از پیشرفتهترین فرآیندهای تولید محصول فولادی است که در صنایع پایین دست زنجیره مانند لوازم خانگی، خودروسازی، ساختمانسازی و… مورد استفاده قرار میگیرد.
با توجه به کاربردهای مهم محصول تولید شده تحت نورد سرد و استفاده از آن برای محصولات ضروری در دنیای مدرن، تجهیزات و ماشینهای به کار رفته در طول این فرآیند نیز باید از فناوری پیشرفته و به روز پشتیبانی کند.
از جمله تجهیزات و ماشینآلات نورد سرد میتوان به موارد زیر اشاره کرد:
- سیستم کنترل برش
- سیستم اندازهگیری نگهدارندهها
- سیستم نقل و انتقال (کویل بازکن، انبار کویل و آکومولاتور)
- تجهیزات مورد استفاده در فرایند شکلدهی فولاد (صافکنندهها، دستگاههای اتصال و سوراخکاری)
- تجهیزات به کار رفته در فرایند پس از شکلدهی (سیستم برش پروفیل)
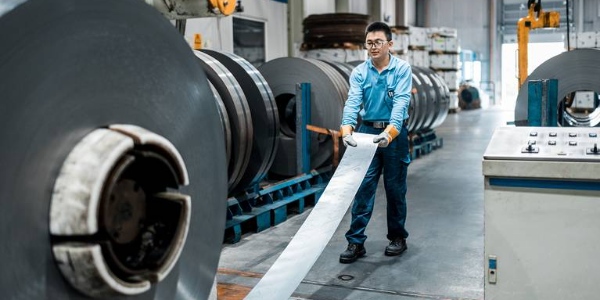
مراحل نورد سرد (ورق سرد)
در ادامه گام به گام مراحل فرآیند نورد سرد را بررسی میکنیم:
1- خطوط اسیدشویی
هدف از این مرحله، پاک کردن پوستههای اکسیدی به وسیله اسید کلریدریک از سطح ورق فولادی است.
2- واحد تاندم میل
پس از اینکه پوستههای اکسیدی از سطح ورق فولادی حذف شد، محصول را برای کاهش ضخامت در دمای محیط به واحد تاندم میل منتقل میکنند. در این مرحله، استفاده از آب و روغن (به عنوان ماده روانساز فولاد) برای ایجاد اصطکاک بالا بین غلطکها جهت کاهش ضخامت ورق ضروری است.
در این واحد معمولا برای کاهش ضخامت ورق به وسیله کشش و فشار زیاد، از پنج قفسه چهار غلتکی (قرار گرفتن ورق در یک امتداد عمودی) استفاده میشود. در نهایت ورق برای تبدیل شدن به کلاف، وارد دستگاه کلاف پیچ میگردد.
۳- واحد نورد دو قفسهای
همانند فرایند واحد تاندم میل، واحد نورد دو قفسهای نیز وظیفه کاهش ضخامت کلاف را برعهده دارد. پس از باز کردن کلاف به وسیله دستگاه کلاف بازکن، محصول از دو قفسه چهار غلطکی عبور میکند تا ضخامت آن را در اثر کشش و فشار زیاد، کاهش دهد. درنتیجه محصول به صورت کلاف درمیآید و به مرحله بعد منتقل میشود.
۴- آنیلینگ یا بازپخت
ورق فولادی وقتی از واحد تاندم میل و واحد نورد دو قفسهای عبور کرد، سختی بالایی به خود میگیرد که پیش از مصرف باید آنیلینگ یا بازپخت شود.
هدف از این مرحله، کاهش ناهمگونی ساختار کریستالی و تنشهای داخلی به همراه نرم کردن سطح ورق از طریق حرارت مجدد در کورههای جعبهای است. فرایند آنیلینگ زمینه را برای انعطافپذیری و شکلپذیری بیشتر ورقها فراهم میکند.
۵- واحد شستشوی الکترولیتی
وظیفه این واحد، رفع هرگونه چربی، آلودگی، پودر آهن و ذرات غیر آهنی جامد از سطح کلاف است. برای انجام این کار، ابتدا محصول را در محلول قلیایی غوطهور میکنند و سپس تحت شستشوی الکترولیتی قرار میدهند.
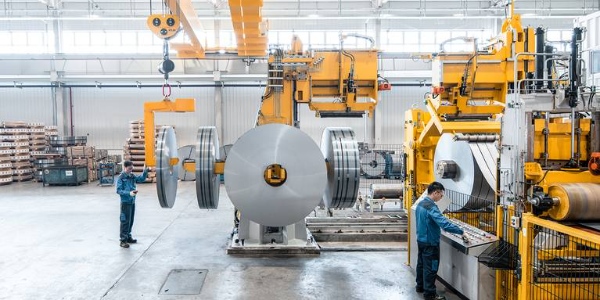
۶- واحد تمپر میل
این واحد دارای دو قفسه چهار غلطکی است که وظیفه دارد سطح ورق را به سختی مورد نظر بر اساس خواص مکانیکی تعیین شده برساند. همچنین واحد تمپر میل ضمن دادن زبری مناسب، وظیفه حذف موج و صاف کردن ورق را نیز برعهده دارد.
۷- واحد قلع اندود
محصول تولید شده در واحد نورد دو قفسهای، به واحد قلع اندود منتقل میشود. در این واحد، علاوه بر کاهش ضخامت کلاف برای مصرف نهایی، سطح ظاهری محصول نیز اصلاح میگردد.
۸- واحد اسکین پاس (نورد پوستهای)
ورقهای فولادی برای ایجاد تنش و کرنش یکنواخت در کنار زبری مجاز، موجگیری، ایجاد سختی و سطحی صاف به همراه رنگآمیزی و لعابکاری، وارد مرحله نورد پوستهای یا اسکین پاس میشود.
۹- کارگاه غلتک
محصول نهایی برای تبدیل شدن به دو شکل کلاف (رول) و ورق (شیت)، وارد کارگاه غلتک میشود. در واقع وظیفه کارگاه غلتک، اصلاح و برش محصول نهایی متناسب با نیاز مشتری است.
خواص مکانیکی ورق نورد سرد
برای تولید ورق فولادی تحت فرآیند نورد سرد، استانداردهایی پیرامون خواص مکانیکی این محصول وجود دارد که بر اساس استاندارد ملی ایران با نام ISIRI ۵۷۲۳ تعریف شده است. برای کسب اطلاعات بیشتر درباره خواص مکانیکی ورق نورد سرد، به جدول زیر مراجعه کنید:
خواص مکانیکی ورق فولادی سرد نوردیده | |||||
کیفیت | تنش تسلیم حداکثر | تنش گسیختگی حداکثر | درصد ازدیاد طول نسبی بعد از شکست | ||
شناسه | نام | L۰=۸۰mm | L۰=۵۰mm | ||
ورق سرد ۱ | معمولی | ۲۸۰ | ۴۱۰ | ۰.۶mm≥۲۷۰.۶mmᐸ۲۸ | ۲۸ |
ورق سرد ۲ | کششی | ۲۴۰ | ۳۷۰ | ۰.۶mm≥۳۳۰.۶mmᐸ۳۴ | ۳۱ |
ورق سرد ۳ | کششی عمیق | ۲۲۰ | ۳۵۰ | ۰.۶mm≥۳۵۰.۶mmᐸ۳۶ | ۳۵ |
ورق سرد ۴ | کشش عمیق آرام شده با آلومینیوم (غیرقابل پیرسختی) | ۲۱۰ | ۳۵۰ | ۰.۶mm≥۳۷۰.۶mmᐸ۳۸ | ۳۷ |
ورق سرد ۵ | کشش بسیار عمیق (فاقد عناصر بین نشین و پایدار شده) | ۱۹۰ | ۳۵۰ | ۰.۶mm≥۳۹۰.۶mmᐸ۴۰ | ۳۸ |
ورق CRS چیست؟
ورق CRS همان ورق روغنی تولید شده در واحد نورد سرد است. ورقهای فولادی نورد سرد دارای خواص برجسته مختلفی از جمله شکلپذیری آسان و سطح صاف و تمیز هستند و در خودروها، لوازم خانگی، مبلمان و بسیاری از اقلام روزمره دیگر استفاده میشوند.
آیا فلزات غیر از فولاد میتوانند نورد سرد شوند؟
فلزاتی مانند تیتانیوم، آلومینیوم و آلیاژهای نیکل به همراه فولاد ضد زنگ، همگی میتوانند تحت نورد سرد قرار بگیرند. علاوه بر این، فلزاتی همچون فولاد گالوانیزه، مس، برنج و برنز نیز قابلیت تولید به واسطه فرآیند نورد سرد را دارند.
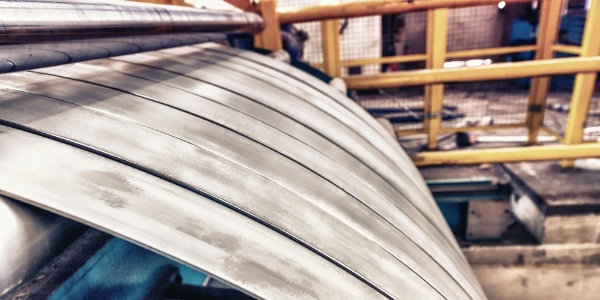
تفاوت نورد گرم و سرد
از جمله مهمترین تفاوتهای ورق تولید شده در طول فرآیند نورد سرد نسبت به نورد گرم میتوان به کاهش ضخامت، افزایش سختی و استحکام محصول نهایی برای استفاده در صنایع مختلف اشاره کرد.
کلام آخر
در این مقاله به موضوع «نورد سرد؛ کاربرد، مزایا و فرایند آن» پرداختیم. نورد سرد ورق فولادی یکی از مراحل تبدیل فولاد به ورقهای نازک برای استفاده در صنایع خودروسازی، ساختمانسازی، لوازم خانگی و غیره است. برای کسب اطلاعات بیشتر و استعلام قیمت روز آهن با ما تماس (۰۲۱۶۷۱۴۵) بگیرید. گروه کارشناسان ما در وبسایت کار آهن، آماده پاسخگویی به سوالات شما عزیزان است.