فولاد ضد زنگ به دلیل مقاومت در برابر خوردگی، حرارت، استحکام بالا، تمیزی و موارد دیگر شناخته میشود. پنج نوع مختلف از فولاد ضد زنگ وجود دارد که تفاوت آنها در ترکیب شیمیایی هر کدام است. فولاد مارتنزیتی نوعی فولاد ضد زنگ است که به دلیل استحکام، مقاومت در برابر خوردگی و دوام شناخته میشود. این ویژگیها، فولاد مارتنزیتی را به انتخاب خوبی برای کاربردهای مختلف تبدیل میکند. در ادامه این مقاله به خواص فولاد مارتنزیتی، ترکیب آن، مزایای آن نسبت به سایر انواع فولاد و کاربردهای آن در صنعت میپردازیم.
زمان خواندن: ۷ دقیقه
فولاد مارتنزیتی چیست؟
فولاد مارتنزیتی نوعی فولاد ضد زنگ است که به دلیل ترکیب شیمیایی آن میتوان از طریق عملیات حرارتی و فرآیند سختشده، آن را تقویت کرد. این روشها فولاد مارتنزیتی را قویتر از سایر انواع میکند که آن را به انتخاب خوبی برای ساخت ابزار پزشکی، شیرهای مکانیکی، قطعات توربین، ابزارهای مکانیکی و سایر کاربردهای مختلف تبدیل میکند.
ترکیب شیمیایی فولاد مارتنزیتی
مانند تمام فولادهای زنگ نزن، جزء اصلی فولاد مارتنزیتی، کروم است که معمولا ۱۱.۵ تا ۱۸ درصد از ترکیب آن را تشکیل میدهد. سایر اجزای رایج شامل ۱.۲ درصد کربن و نیکل میشود. مقدار بالای کربن به این نوع فولاد ساختار مولکولی قدرتمند میبخشد اما کمبود نیکل باعث میشود که مقاومت کمتری در برابر خوردگی نسبت به سایر انواع فولاد ضد زنگ داشته باشد. مقادیر کمی از عناصر آلیاژی دیگر مانند منگنز، مولیبدن و نیکل نیز اضافه به ترکیب شیمیایی آن اضافه میشود.
معرفی انواع فولاد ضد زنگ مارتنزیتی
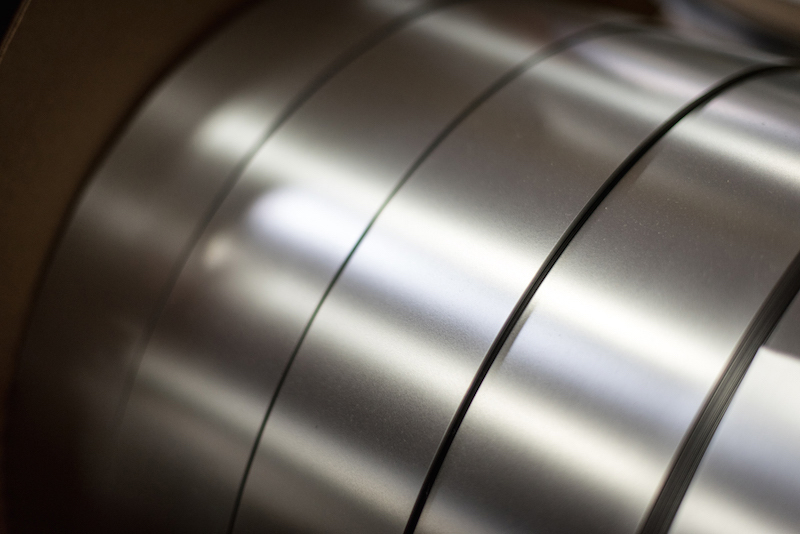
رایجترین انواع ورقهای فولادی مارتنزیتی شامل ۴۱۰ Stainless Steel، ۴۲۰ Stainless Steel و ۴۴۰A میشود. این فولادهای ضد زنگ مارتنزیتی مانند آلیاژهای فولادی با کربن بالا به عملیات حرارتی واکنش نشان میدهند. حداکثر سختی خاموش شده در درجه اول به محتوای کربن بستگی دارد. همچنین آنها با حرارت دادن به دماهای بالا و سپس سرد شدن سریع سخت میشوند.
از آنجایی که ساختار مارتنزیتی سخت شده کاملا شکننده است، معمولا در دماهای پایین مجددا گرم میشود تا ریزساختار را کاهش دهد. یا دوباره تا دمای کمی بالاتر گرم میشود تا مواد تا سطوح سختی متوسط نرم شوند. بازپخت فرآیندی با حرارت دادن درست زیر دمای بحرانی آلیاژها انجام میشود. در واقع بازپخت کامل با حرارت دادن درست بالاتر از دمای بحرانی با خنک شدن کندتر حاصل میگردد.
انواع فولاد مارتنزیتی
فولاد مارتنزیتی را میتوان بر اساس محتوای کربن به دو نوع مجزا تقسیم کرد.
۱- فولاد مارتنزیتی کم کربن
فولاد مارتنزیتی کم کربن دارای محتوای کربن بین ۰.۰۵ تا ۰.۲۵ درصد است. نسخههای کم کربن فولاد مارتنزیتی قویتر هستند، مقاومت در برابر خوردگی بالاتری داشته و پتانسیل بیشتری برای ساخت دارند.
۲- فولاد مارتنزیتی با کربن بالا
فولاد مارتنزیتی پر کربن معمولا دارای محتوای کربن بین ۰.۶۱ تا ۱.۵۰ درصد است. افزایش محتوای کربن فولاد را قویتر میکند؛ زیرا کربن ساختار مولکولی فولاد را تقویت میسازد. با این حال، فلز را شکنندهتر میکند و نمیتوان آن را جوش داد یا به راحتی به اشکال دیگر درآورد.
۳- فولاد ضد زنگ ۴۱۰
فولاد ضد زنگ نوع ۴۱۰ یک نوع فولاد ضد زنگ مارتنزیتی است که به عنوان یک مارتنزیتی برای مصارف عمومی در نظر گرفته میشود. کاربردها شامل اتصالدهندهها، فنرها، پینها، کارد و چنگال، سخت افزار، گیرههای تفنگ، قطعات میکرومتری، تیغههای توربین، صفحههای زغال سنگ، میلههای پمپ، مهرهها، پیچها، اتصالات، بلبرینگها، شفتها، پروانهها، پیستونها و شیرها است. سطوح سختی را میتوان با تغییرات جزئی در عملیات حرارتی سخت و سرد شدن تغییر داد.
۴- فولاد ضد زنگ ۴۲۰
فولاد ضد زنگ نوع ۴۲۰ محدوده کربن وسیعی از ۰.۱۵ تا ۰.۴۵ درصد محتوای کربن را پوشش میدهد و بنابراین دارای طیف نسبتا گستردهای از سطوح سختی در هر دو حالت سخت شده و سکوریت شده است. برخی از کاربردهای فولاد ضد زنگ ۴۲۰ شامل اتصالدهندهها، کارد و چنگال، قطعات ماشینآلات، بوشها، ابزارهای جراحی، اسلحههای گرم و موارد تزئینی میشود.
۵- فولاد ضد زنگ ۴۴۰
فولاد ضد زنگ نوع ۴۴۰A قابلیت سخت شدن بیشتری نسبت به نوع ۴۱۰ یا نوع ۴۲۰ دارد، اما شکلپذیری محدودی در شرایط آنیل شده از خود ارائه میدهد. این گرید از فولاد ضد زنگ تا بیش از RC50 قابل سخت شدن است که آن را در کاربردهای صفحات تیغهای بسیار جذاب میکند. سختی بالای این گرید به این معنی است که تیغهها برای مدت طولانیتری تیز میمانند.
کاربردهای این نوع گرید شامل کارد و چنگال، ابزار جراحی و بلبرینگ است. همچنین نوع ۴۴۰A در کاربردهای دیگری که سختی بالا در کنار مقاومت در برابر خوردگی مهم است، استفاده می شود
سایر گریدهای فولاد مارتنزیتی
گریدهای مارتنزیتی ذکر شده در بالا رایجترین گریدهایی هستند که در دسترس و مورد استفاده قرار میگیرند. سایر گریدهای مارتنزیتی با الزامات ترکیب شیمیایی خاص و یا خواص مکانیکی نیز در بازار موجود است اما وقتی در مورد مارتنزیتی صحبت میشود، ۴۱۰، ۴۲۰ و ۴۴۰ گریدهایی هستند که بیشتر به آنها اشاره میشود.
ویژگیهای فولاد مارتنزیتی
فولاد مارتنزیتی علاوه بر استحکام، دارای خواص متعددی است که آن را از سایر انواع فولاد ضد زنگ متمایز میکند. گریدهای مارتنزیتی فولادهای زنگ نزن طیف وسیعی از کاربردها، از مقاومت در برابر خورندگی نسبتا کم تا ایجاد حداکثر استحکام و سختی برای قطعات سرد شکل را پوشش میدهند.
دیگر ویژگیهای این نوع فولاد عبارتند از:
۱- قابلیت جوشکاری
فولاد مارتنزیتی معمولا شکننده است و در اکثر فرمها واکنش مطلوبی به جوشکاری ندارد. با این حال، فولاد مارتنزیتی کوئنچ و تمپر شده، شکنندگی آن را کاهش داده و کاربردهای آن را افزایش میدهد. فرآیند کوئنچ و تمپر شامل حرارت دادن فلز و سپس سرد کردن سریع آن برای قرار گرفتن در جای خود است. فولادهای زنگ نزن مارتنزیتی با کربن بالا معمولا برای جوشکاری توصیه نمیشوند، اگرچه نوع ۴۱۰ Stainless را میتوان با سهولت نسبی جوش داد.
۲- خاصیت مغناطیسی
بسیاری از انواع فولاد مارتنزیتی خاصیت مغناطیسی دارند. اگر آهن در آلیاژ وجود داشته باشد، ساختار مولکولی کریستال مانند میتواند مغناطیسی باشد. مغناطیس دستهبندی فلزات را آسانتر کند اما میتواند جوشکاری و سایر فرآیندهای ساخت را دشوارتر نماید. فولادهای مارتنزیتی در هر دو حالت آنیل شده و سخت شده، خاصیت مغناطیسی دارند.
۳- شکلپذیری
شکلپذیری توانایی فلز برای تبدیل شدن به اشکال مختلف بدون شکستن یا ترک خوردن است. با افزایش محتوای کربن، شکلپذیری فولاد مارتنزیتی کاهش مییابد. اشکال کم کربن برای شکل دادن ایدهآل نیستند، اما همچنان میتوان تا حدودی آنها را شکل داد.
۴- استحکام بالا
فولادهای زنگ نزن مارتنزیتی در درجه اول جایی که خواص مکانیکی بالا ضروری است، استفاده میشوند. مقاومت به خوردگی آنها بیشتر از سایر آلیاژهای خانواده فولاد زنگ نزن، عامل محدود کننده در کاربرد آنها است.
اغلب، مقداری لکه سطحی زنگ زده روی سطوح آنها ظاهر میشود. هنگامی که فقط به مقاومت خوردگی محدود یا مقاومت در برابر پوسته پوسته شدن دمای بالا نیاز باشد، میتوان از آنها در شرایط آنیل شده نیز استفاده کرد اما بالاترین مقاومت خوردگی در شرایط سخت شده یا تمپر شده به دست میآید.
فولاد ضد زنگ مارتنزیتی آنیل شده
گریدهای مارتنزیتی معمولا در شرایط آنیل شده به تولیدکنندگان عرضه میشوند؛ زیرا این حالت بهترین ویژگیهای شکلدهی را فراهم میکند. عملیات حرارتی سخت شدن به طور کلی پس از عملیات شکلدهی انجام میشود.
درمقایسه با فولادهای زنگ نزن آستنیتی سری ۳۰۰، میتوان در شرایط سرد کار در سطوح مقاومت کششی نسبتا پایین نیز به گریدهای ۴۱۰ و ۴۲۰ دست یافت.
تفاوت فولاد مارتنزیتی با انواع فولاد ضد زنگ
همانطور که قبلا گفته شد، انواع فولاد ضد زنگ در ساختار شیمیایی و اجزای آنها متفاوت هستند. این عوامل رفتار فولادها و کاربردهای احتمالی را تعیین میکنند.
این نوع فولاد در مقایسه با سایر انواع فولاد ضد زنگ دارای محتوای کروم بالایی است. آنها همچنین از نیتروژن، منگنز و نیکل تشکیل شدهاند. این باعث میشود تا در برابر خوردگی بسیار مقاوم باشند و یکی از پرکاربردترین انواع فولادهای زنگ نزن به حساب بیایند. برخلاف فولاد مارتنزیتی، فولاد آستنیتی جوشپذیر، شکلپذیر است.
کلام آخر
بسیاری از ویژگی های منحصر به فرد فولاد ضد زنگ آن را برای تعدادی از کاربردهای مختلف ایدهآل میکند. انواع مختلفی از فولاد ضد زنگ وجود دارد که در پنج دسته اصلی قرار می گیرند. فولاد ضد زنگ مارتنزیتی یک فولاد همه کاره است که کاربردهای عملی زیادی برای صنایع مختلف دارد. این نوع فولاد به اشکال مختلف عملیات حرارتی که میتواند استحکام، سختی و مقاومت در برابر خوردگی را افزایش دهد، جواب میدهد. استحکام فولاد ضد زنگ مارتنزیتی و مقاومت در برابر خوردگی میتواند برای کاربردهای دریایی، صنعتی و پزشکی ایدهآل باشد.