اولین دستگاه نورد توسط لئوناردو داوینچی ساخته شده است. اگرچه خیلی از پژوهشگران تاریخ این موضوع را رد میکنند اما باید تاکید کرد که عملیات نورد فولاد برای نخستین بار در قرن هفدهم آغاز شد که به مروز و با گذر تاریخ از انقلاب صنعتی و رسیدن به عصر مدرن، این فرآیند پیشرفتهای گستردهای به چشم دید. در این مقاله قصد داریم درباره نورد، نوردکاری، انواع نورد و تفاوت نورد سرد و گرم صحبت کنیم. برای خواندن ادامه مطلب، مجله کارآهن را دنبال کنید.
نورد چیست؟
برای پاسخ به این پرسش که نورد چیست یا نورد کاری چیست، باید اشاره کنیم که در فلزکاری، عبور فولاد مذاب شده از یک یا چند جفت غلتک برای کاهش ضخامت، به عنوان نورد شناخته میشود. به عبارت دیگر، نورد در فلزکاری شامل فرآیند شکلدهی است که به کاهش و یکنواخت شدن ضخامت فلز کمک میکند.
این فرایند بر اساس دمای فلز طبقهبندی میشود؛ اگر دمای فلز بالاتر از دمای تبلور مجدد باشد، نورد گرم است. در حالی که اگر دمای فلز کمتر از دمای تبلور مجدد باشد، به این فرآیند نورد سرد میگویند.
بیشتر بخوانید:
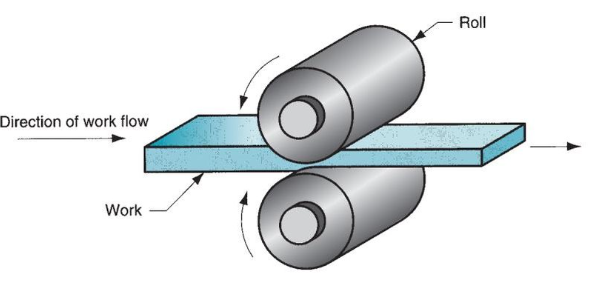
تاریخچه نورد
عملیات نورد صدها سال است که پدید آمده است. اولین عملیات نورد کوچک و با دست بودند و برای صاف کردن طلا و نقره به ویژه جواهرات و آثار هنری به کار میرفتند.
در سال ۱۴۸۰، لئوناردو داوینچی ماشینی جهت نورد کردن سرب برای شیشههای رنگی طراحی کرد. این اولین رکورد ثبت شده کارخانه نورد در جهان است؛ با این حال هیچ مدرکی دال بر ساخت این دستگاه توسط داوینچی وجود ندارد.
در اواسط قرن پانزدهم آسیابهای کوچک، توری طلا و سایر کارهای تزئینی را تولید میکردند. با این حال، همانطور که این تکنیکها به طور گستردهای پیش میرفت، تقاضا برای محصولاتی که از نورد فلز تولید میشدند، افزایش یافت. در ضمن شواهدی مبنی بر نورد سرب و قلع بر روی آسیابهای ساده با غلتکهای چدنی در آغاز قرن هفدهم وجود دارد.
در دهه ۱۶۰۰، ماشینهای نورد، جایگزین غلتکهای کوچک و دستی شدند و در این حول و حوش زمانی بود که آهن به عنوان فلزی با قابلیت نورد معرفی شد. در اواخر دهه ۱۷۰۰، اولین کارخانههای نورد گرم پدید آمدند و همین امر به فلز اجازه داد تا تحت این عملیات، در صنایع بیشتری مورد استفاده قرار گیرد.
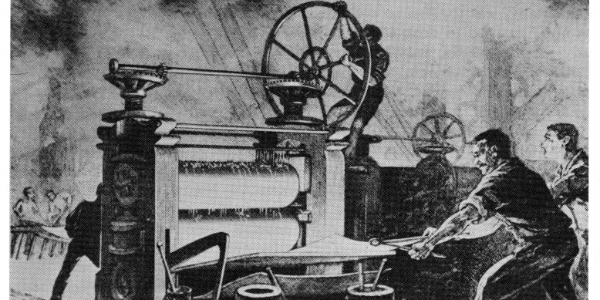
انقلاب صنعتی (۱۷۶۰ تا ۱۸۴۰) تقاضای بیسابقهای برای محصولات آهنی ایجاد کرد. فناوری جدید برای ساخت آهن و در نهایت فولاد اختراع شد و فلزات در محصولات جدید مانند ماشینآلات، راه آهن و کشتیهای بخار مورد استفاده قرار گرفتند.
در این مرحله، کارخانههای نورد، نمیتوانستند حجم بالایی از فلز را که امروزه میبینیم، تولید کنند. به علاوه اینکه، اگر با استانداردهای دقیق امروزی بسنجیم، کیفیت مورد نیاز محصولات اولیه قدرت چندانی نداشت و اصطلاحا «ضعیف» بود.
با این حال اگر قرار بود این فناوری بیشتر گسترش مییافت، تامین انرژی به عنوان یک مانع بزرگ پیش روی این تحول قرار داشت. بنابراین عملیات نورد به مرور به سطحی از فناوری رسید که امروزه میتوان به راحتی و در حجم انبوه، فلزات مختلف را تحت دو روش نورد سرد و گرم تولید کرد.
فرآیند نورد چگونه است؟
در ادامه پاسخ به این پرسش که «نورد چیست؟» باید بگوییم که یکی از کاربردهای عملیات نورد، کاهش ضخامت شمشهای فولادی است؛ بدین صورت که با عبور شمش از بین دو غلتک، ضخامت آن کم و طول آن زیاد میشود. در صورتی که این فرایند در دمای بالاتر از تبلور مجدد انجام شود، نورد گرم و در دماهای پایین، نورد سرد نامگذاری میگردد
لازم به توضیح است که در عملیات کاربردی نورد، فرایندهای نورد سرد دارای تناژ بیشتری نسبت به فرایند نورد گرم است. با این حال در ادامه به توضیح انواع نورد کاری و تفاوت نورد گرم و سرد میپردازیم.
انواع نوردکاری
بهطور کلی، نوردکاری به دو دسته نورد گرم و نورد سرد تقسیم میشود.
نورد گرم
همانطور که پیشتر در پاسخ به این پرسش که نورد چیست گفته شد، در فرآیند فلزکاری، نورد گرم بالاتر از دمای تبلور مجدد مواد رخ میدهد. محصولات تولید شده در این فرآیند، شامل انواع مقاطع فولادی مانند میلگرد و ورق فولادی مورد استفاده در لولههای خطوط انتقال نفت، گاز و آب است.
نورد سرد
بر خلاف نورد گرم، نورد سرد کمتر از دمای تبلور مجدد مواد، معمولا در دمای اتاق رخ میدهد. این امر باعث افزایش استحکام تا حدود ۲۰ درصد بیشتر (از طریق سخت شدن کرنش) شده و سطح فلز را صاف و صیقلی میکند.
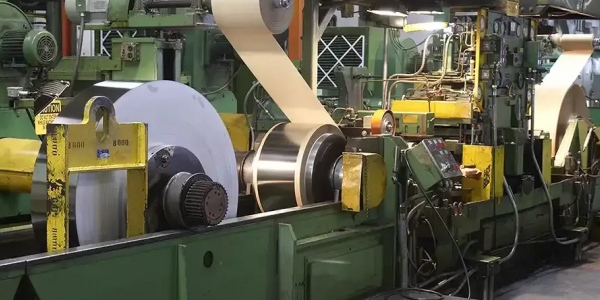
مقایسه نورد گرم و سرد
ویژگیها | نورد گرم | نورد سرد |
دمای عملیاتی | بین ۹۰۰ تا ۱۳۰۰ درجه سانتیگراد | بین ۲۰ تا ۹۰ درجه سانتیگراد |
نوع مواد قابل نورد | فلزات آهنی و غیرآهنی، فولادهای سخت، فولادهای روی آلیاژی، مس و آلومینیوم | فولادهای کم کربن، فولادهای ضد زنگ، آلومینیوم و مس |
میزان سختی | کمتر | بیشتر |
اندازه دقیق و شکل دقیق | اندازه دقیق و شکل دقیق قطعات نورده شده | عدم دقت در اندازه دقیق و شکل دقیق قطعات نورده شده |
روش کار | به روش نوساندهی | به روش افزایش فشار |
ضریب شکلدهی | بالاتر | پایینتر |
شکلدهی | ضخامت قطعه در نورد گرم بیشتر است و امکان شکل دهی به قطعات بزرگتر وجود دارد. | شکل دهی به قطعات نازک و دقیق با تحمل خطای کمتر امکانپذیر است. |
کیفیت سطح | دارای اکسید و زنگ | سطح صاف و صیقلی |
زمان تولید | سرعت بالاتر | سرعت پایینتر |
هزینه | هزینهبیشتر برای ماشین آلات و انرژی | هزینه کمتر برای ماشینآلات و انرژی |
ابعاد قطعه | ابعاد بزرگتر | ابعاد کوچکتر |
خواص مکانیکی | خواص مکانیکی ضعیفتر از نورد سرد، اما به دلیل تنشهای ناشی از نورد گرم، قطعاتی با مقاومت بالا به تغییر شکل پایدارتر دارند. | خواص مکانیکی بهتر در مقایسه با نورد گرم. |
کاربردها | مناسب برای تولید قطعات بزرگ و ضخیم مانند بلوکهای موتور، تیرآهن و نبشیهای فولادی | مناسب برای تولید قطعات نازک و دقیق مانند ورقها و لولههای فلزی. |
مزایا و معایب نورد گرم و سرد
ویژگیها | نورد گرم | نورد سرد |
مزایا | عملیات سریعتر و موثرتر برای قطعات بزرگ و ضخیم تحمل بهتر تنشهای ناشی از فرایند نورد قیمت مناسبتر | قابلیت تولید قطعات با شکل دقیق و اندازه دقیق عملیات نورد با کیفیت بالا برای قطعات نازک و دقیق کاهش تولید ضایعات |
معایب | تغییر شکل به دمای بالا که ممکن است باعث تغییر خواص مکانیکی قطعات شوددشواری در کنترل اندازه دقیق و شکل دقیق قطعاتکیفیت سطحی پایینتر نسبت به نورد سرد | عملیات زمانبر و هزینهبر برای قطعات بزرگ و ضخیم شکنندگی و شکستپذیری بیشتر قطعات نورده شده در مقایسه با نورد گرم |
انواع نورد از لحاظ کاربرد
علاوه بر تقسیمبندی نورد به دو دسته نورد گرم و سرد، میتوان آن را از لحاظ کاربرد نیز تقسیم کرد:
۱. نورد مقاطع
در نورد مقاطع، فرم غلتکها به صورت عمود بر فلز است تا ضمن عبور فلز از غلتکهای شیاردار، کاهش سطح مقطع اتفاق بیفتد. این فرایند برای تولید انواع مقاطع مانند تیرآهن، میلگرد، ورق فولادی، لوله، نبشی، ناودانی و… مورد استفاده قرار میگیرد.
۲. نورد عرضی
در فرایند نورد عرضی، غلتکهای موازی با حرکت فلز کار میکنند.
۳. نورد طولی
فرایند نورد طولی به این صورت است که چرخش غلتک پایین در جهت ساعت و چرخش غلتک بالایی به صورت پاد ساعتگرد حرکت میکند. همچنین در نورد طولی، محور غلتکها عمود بر جهت حرکت فلز است تا همین امر زمینه را برای کاهش ضخامت ورق به وجود آورد.
لازم به توضیح است که پهنای ورق بیشتر از ضخامت آن در نظر گرفته میشود؛ به طوری که پهنای ورق پس از اتمام عملیات نورد، هیچ گونه تغییری نمیکند. همچنین نورد طولی به صورت عمومی در تولید ورقهای فولادی مورد استفاده قرار میگیرد.
۴. نورد پیچی
در نورد پیچی، محور غلتکها به صورت ناموازی است؛ به طوری که برای حرکت فلز، از یک حرکت حلزونی استفاده میشود. این فرایند برای تولید فولاد مورد استفاده در انواع لوله کاربرد دارد.
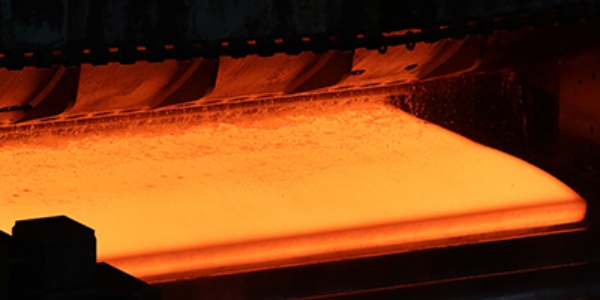
فرآیند نورد از نظر دمای عملیات
فرایند نورد از نظر دمای عملیات، به دو بخش نورد گرم و نورد سرد تقسیمبندی میشود. عملیات نورد گرم به صورتی است که به راحتی میتوان فلز را به هر شکلی که نیاز باشد، تغییر داد. با توجه به اینکه در اثر تبلور مجدد، استحکام تسلیم در فلز تحت نورد گرم کاهش مییابد؛ بنابراین در این فرایند نیروی لازم برای قطعات بزرگ، افت محسوسی پیدا میکند.
از طرفی نورد سرد برای تغییر شکل نهایی فلز مورد استفاده قرار میگیرد که اصطلاحا دارای یک سطح مطلوب برای استفاده در صنایع پایین دست زنجیره فولاد است.
دستگاه نورد و انواع آن
یکی از اهداف مهم غلتکهای مورد استفاده در عملیات نورد پیرامون این پرسش که «نورد کاری چیست»، اعمال نیروی لازم به شمش فولادی برای ایجاد نیروی چرخشی، تغییر شکل در ابعاد و غیره است.
برای این منظور، غلتکها باید بر روی تجهیزات یا همان دستگاه نورد قرار گیرد. دستگاهی که غلتکها بر روی آن قرار میگیرند را قفسه مینامند. قفسهها به ۴ شکل است که شامل قفسه دو غلتکی، قفسه سه غلتکی، قفسه چهار غلتکی و قفسه شش غلتکی میشود.
غلتکهای مورد استفاده در قفسهها به ۲ نوع قفسه نورد مداوم و قفسه نورد غیر مداوم تقسیمبندی میشوند. در نورد مداوم، شمش به صورت هم زمان در چندین قفسه قرار گرفته و به صورت کاملا یک طرفه حرکت میکند.
لازم به توضیح است که برای نورد مداوم مقاطع فولادی، قفسهها به صورت افقی و عمودی (یک در میان) قرار میگیرند تا از این طریق بتوان ضخامت و پهنای شمش فولادی را به صورت یکنواخت کاهش داد.
نورد غیر مداوم یا نورد رفت و برگشتی دارای ۳ غلتک و چندین کالیبر است. در هر مرحله از این فرآیند، شمش فولادی از کالیبرها عبور میکند و سپس حرکت غلتکها برعکس شده و شمش را ۹۰ درجه چرخانده و از سمت کالیبر دیگر برمیگردد. لازم به ذکر است که در مسیر برگشت شمش، فاصله میان غلتکها به حداقل ممکن میرسد.
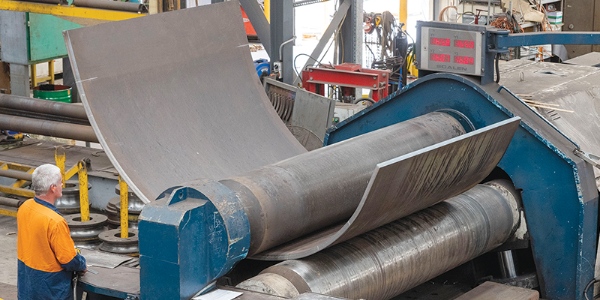
نورد پیوسته
وقتی تنشهای کششی بزرگی به ورق فولادی وارد شود تا ضمن کشیده شدن، ضخامت آن کاهش و طول آن افزایش پیدا کند، اصطلاحا به این فرآیند «نورد پوستهای» یا «اسکین پاس رولینگ» میگویند. نورد پوستهای به طور معمول به وسیله قفسههای دو و چهار غلتکی انجام میشود.
نورد چهار غلتکی شامل ۲ غلتک با سایز کوچک و دو غلتک پشتیبان در سایز بزرگتر است. این در حالی است که نورد دو غلتکی دارای ۲ غلتک بزرگ است که در عملیات نورد مورد استفاده قرار میگیرد.
یکی از مزیتهای مهم فرایند نورد پوستهای در خط نورد، افزایش خواص مکانیکی به همراه بالا بردن کیفیت سطح فلز یا ورق فولادی (بدون اعوجاج) مورد نظر است. به طوری که با آغاز فرآیند کششی ورق و تغییر فرم پلاستیک آن، خزش فلز در لبه محصول حذف میشود؛ زیرا که این نوع خزش در حین کشش ورق، زمینه را برای عیوب سطحی محصول به وجود میآورد. بنابراین نورد پوستهای میتواند تمام عیوب سطحی فلز را در عملیات نورد گرم تصحیح یا بهبود بخشد.
علاوه بر این، نورد پوستهای سبک نوارهای آنیل شده فولاد، از کرنشهای کششی و شکست عرضی محصول جلوگیری به عمل میآورد؛ زیرا به واسطه عملیات خم کردن و کشش عمیق فولاد نرم آنیل شده، امکان بروز چنین مشکلاتی برای فلز وجود دارد.
لازم به توضیح است که اغلب نوارهای فولاد کم کربن آنیل شده به علت نرم بودن در شرایط آنیل، تحت عملیات نورد پوستهای قرار میگیرند.
نورد حلقهای
فرایند نورد حلقهای برای کاهش یا افزایش ابعاد فلز مورد استفاده قرار میگیرد. روش انجام این فرایند به گونهای است که حلقهها در بین دو غلتک قرار گرفته تا این وسیله بتواند برای نازک کردن سطح حلقه، روی آن بچرخد. این مرحله به طور معمول با استفاده از غلتکهای شکلدار در انواع مقاطع فولادی استفاده میشود.
نورد خوشهای
وقتی ورق فولادی بیش از اندازه نازک است (مانند فویل)، از نورد خوشهای با غلتکهای کوچک استفاده میگردد. تعداد غلتکهای کوچک در این فرایند، بیشتر از سایر روشها در نظر گرفته میشود؛ به طوری که امکان بروز مشکلاتی مانند کج شدن یا تاب برداشتن غلتک وجود دارد. برای حل این مشکل، غلتکهای بزرگ را برای پوشش بر روی غلتکهای کوچک قرار میدهند.
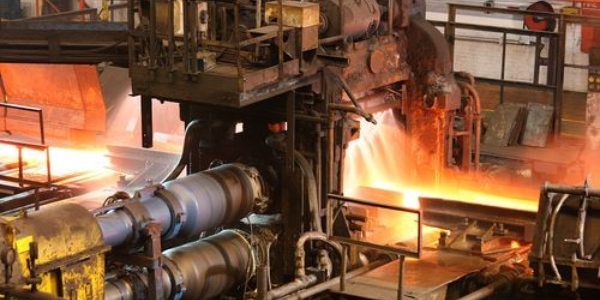
نورد رزوه
در فرایند نورد رزوه که برای شکلدهی فلز در حالت سرد صورت میگیرد، از دو غلتک تخت در کنار یکدیگر استفاده میکنند. محصول فولادی بین دو غلتک قرار میگیرد تا به واسطه یک حرکت سایشی، رزوهها را به وجود آورد.
نورد رزوهای نسبت به مدلهای ریختهگری و تراشکاری، نه تنها استحکام بیشتری دارد بلکه از نظر انرژی مصرفی، مدت زمان و قیمت نهایی نیز دارای برتری است.
از جمله کاربردهای نورد رزوه میتوان به تولید میلگرد، چرخدنده، بلبرینگ، پیچ، رزوهها و کوره دوار ذوب مس، کورهها و بدنه هواپیما اشاره کرد.
نورد آهن چیست؟
عملیات نورد آهن شامل کاهش سطح مقطع فولاد است که بر اساس آن، کاهش سطح مقطع صورت میگیرد. این فرآیند به دو صورت نورد سرد و گرم انجام میشود که هر کدام بر اساس کاربرد، در صنایع مختلف به کار میرود.
این فرایند شامل عبور آهن از چندین غلتک است که با سرعت یکسان (اما در جهت مخالف یکدیگر) میچرخند و فاصله آنها کمی کمتر از ضخامت فلز در نظر گرفته میشود.
نورد میلگرد چیست؟
میلگرد ساختمانی تقریبا در هر سازه بتن آرمه صنعت ساختمانسازی یافت میشود. این محصول به عنوان نوار تقویتی سازه، به میلههای فولادی اطلاق میشود که در داخل بتن نصب میگردد تا به آنها کمک کند شکل و مقاومت خود را تحت شرایط کاربردی حفظ کنند.
میلگرد معمولا از فولاد کربنی تشکیل شده است؛ زیرا این ماده امکان اتصال قویتر با بتن و استحکام کششی آن را تضمین میکند. انواع میلگرد ساختمانی از نظر شکل ظاهری به میلگرد ساده/آجدار و شاخهای/کلافی تقسیمبندی میشود که تحت استاندارد A۲ ،A۱ و A۳ تولید میگردد.
همچنین میلگردهای ساختمانی-سازهای از لحاظ کیفی در چهار نوع نورد گرم، نورد سرد، ترمکس و میکروآلیاژی تقسیمبندی میشود. در ضمن انواع میلگرد موجود در بازار از نظر نوع پوشش به صورت میلگرد ساده، گالوانیزه، اپوکسی، کامپوزیت و… نیز تولید میشوند که در مورد میلگردهای ساختمانی-سازهای کاربرد چندانی ندارند.
با این حال بتن یک ماده ارتجاعی است که میتواند مقدار قابل توجهی وزن را تحمل کند اما آنچه که در ظرفیت باربری خود ارائه میدهد، فاقد استحکام کششی است. بنابراین با اضافه کردن میلگرد به بتن، استحکام کششی بتن نیز افزایش پیدا میکند.
میلگرد در انواع سایز و تحت استانداردهای مختلف تولید میشود که شما میتوانید برای اطلاع از قیمت لحظه ای میلگرد به وب سایت کارآهن مراجعه کنید.
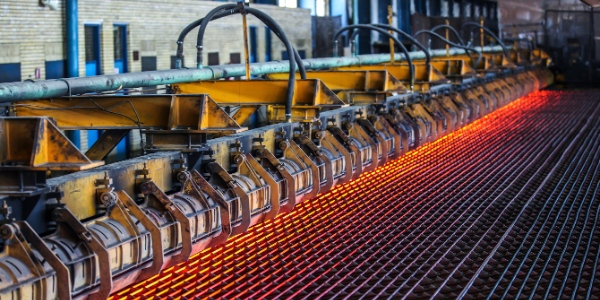
کاربرد فرآیند رولینگ میلگرد
رولینگ میلگرد همان نورد گرم میلگرد است که با هدف تبدیل شدن به قطر و سایز مورد نیاز، مورد استفاده قرار میگیرد. میلگردهای فولادی یا میلگردهای تقویتکننده، میلههایی هستند که در ساخت بتن برای استحکام کششی، خمشی و برشی بتن مسلح استفاده میشوند. آنها معمولا برای جلوگیری از لغزش در داخل بتن، آجدار هستند و مزایای متعددی مانند بهبود مقاومت سازه بتنی را به همراه دارند.
نورد تیرآهن چیست؟
نورد تیرآهن به دو صورت نورد گرم و نورد سرد انجام میشود. نورد گرم تیرآهن شامل فرایندی است که محصول ضمن رسیدن به دمای مومسانی (۱۰۰۰ تا ۱۲۵۰ درجه سانتیگراد)، برای تغییر ابعادی و سطحی از غلتکهای دستگاه نورد عبور میکند.
پس از انجام این مرحله، شمش فولادی برای تغییر سطح مقطع وارد قفسه نورد میشود. در نهایت شمش برای خنک شدن، تحت فشار آب قوی قرار میگیرد.
تیرآهن نورد سرد نه تنها ابعاد کوچک تری نسبت به تیرآهن نورد گرم دارد بلکه به واسطه بالا بودن کربن، از استحکام و دوام بیشتری برخوردار است. در نتیجه فرآیند نورد سرد تیرآهن قیمت بالاتری نسبت به نورد گرم بر روی دست تولیدکننده میگذارد.
مهمترین تفاوت نورد گرم و سرد تیرآهن، انعطافپذیری بیشتر و سهولت ساخت و قیمت مقرون به صرفه است. از جمله کاربردهای تیرآهن تولید شده طی عملیات نورد گرم میتوان به صنعت ساختمانسازی و ریل راه آهن اشاره کرد.برای اطلاع از قیمت روز تیرآهن، به وبسایت کارآهن مراجعه کنید.
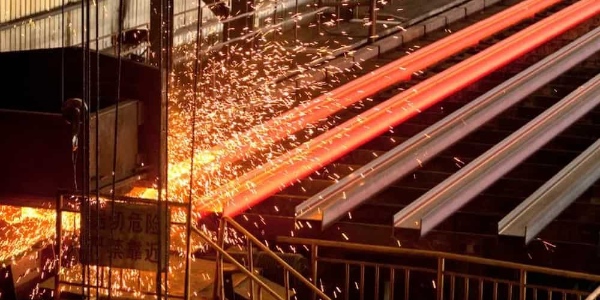
کلام آخر
عملیات نورد شامل فرایندی است که به واسطه آن میتوان علاوه بر کاهش ضخامت یا سطح مقطع فلز، انعطافپذیری، استحکام و دوام محصول را نیز افزایش داد. مهمترین تفاوت نورد گرم و سرد در کاربردهایی است که برای آن در نظر میگیرند. زیرا نورد گرم انعطافپذیری فلز را بیشتر میکند؛ در حالی که نورد سرد، زمینه را برای بالا بردن استحکام و دوام محصول نهایی به وجود میآورد.برای کسب اطلاعات بیشتر درباره این موضوع و استعلام قیمت آهن آلات، با ما تماس بگیرید. گروه کارشناسان ما در وب سایت کار آهن، آماده پاسخگویی به سوالات شما عزیزان هستند.